Checking Out the Various Methods and Technologies Behind Plastic Extrusion
The world of plastic extrusion is a mix of innovation, technology, and precision, crucial to countless industries worldwide - plastic extrusion. Advanced machinery, computerized controls, and an array of products merge in this complicated process, creating premium, long lasting products. As the market progresses, a shift towards lasting products and smart equipment appears. The adhering to conversation will clarify these technologies and strategies, while likewise meaning the interesting future prospects of this essential production procedure.
Comprehending the Fundamentals of Plastic Extrusion
The process of plastic extrusion, commonly hailed as a keystone in the world of production, develops the bedrock of this conversation. In significance, plastic extrusion is a high-volume production procedure in which raw plastic product is melted and developed into a constant profile. The process starts with feeding plastic products, often in the kind of pellets, right into a warmed barrel.
The Role of Different Materials in Plastic Extrusion
While plastic extrusion is a frequently made use of method in production, the materials utilized in this procedure substantially affect its last output. Various sorts of plastics, such as polyethylene, abdominal muscle, and pvc, each offer special homes to the end product. For instance, polyethylene, recognized for its toughness and flexibility, is frequently used in product packaging, while PVC, renowned for its stamina and resistance to environmental aspects, is utilized in building. ABS, on the other hand, combines the finest characteristics of both, leading to high-impact resistance and strength. The selection of material not just impacts the item's physical properties yet also influences the extrusion speed and temperature. As a result, producers need to thoroughly take into consideration the properties of the product to maximize the extrusion process.
Strategies Made Use Of in the Plastic Extrusion Refine
The plastic extrusion procedure involves various techniques that are essential to its operation and efficiency (plastic extrusion). The conversation will begin with a simplified description of the essentials of plastic extrusion. This will be complied with by a break down of the process thoroughly and an expedition of methods to improve the efficiency of the extrusion technique
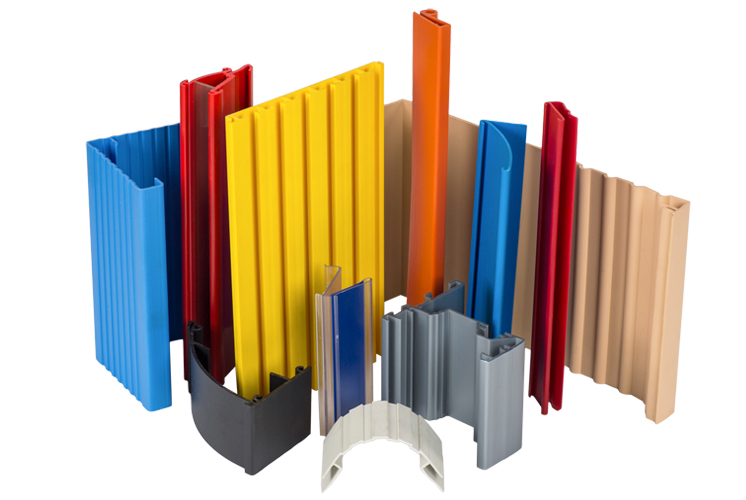
Recognizing Plastic Extrusion Essentials
In the realm of manufacturing, plastic extrusion stands as a basic procedure, necessary in the production of a wide variety of day-to-day items. At its core, plastic extrusion involves transforming raw plastic product right into a continuous profiled shape. This is accomplished by thawing the plastic, usually in the type of granules or pellets, and forcing it through a designed die. The resulting product is a long plastic piece, such as a pipe, wire, or panel finishing, that maintains the form of the die. This cost-efficient method is extremely flexible, able to produce complicated shapes and accommodate a variety of plastic products. Fundamental understanding of these basics enables further exploration of the more intricate aspects of plastic extrusion.
Detailed Extrusion Refine Malfunction

Improving Extrusion Method Efficiency
Performance gains in the plastic extrusion process can dramatically affect both the quality of the last item and the general performance of the operation. Constant optimization of the extrusion technique is important to maintaining an one-upmanship. Methods that boost performance commonly involve exact control of temperature level and pressure throughout the process. Modern innovations, such as digital systems and sensing units, have actually contributed in achieving this control. The usage of top quality raw products can minimize waste and boost output top quality. Regular upkeep of extrusion tools can also minimize downtimes, thus increasing efficiency. Finally, taking on lean production principles can help get rid of unneeded actions in the procedure, advertising effectiveness gains.
Just How Modern technology Is Altering the Face of Plastic Extrusion
The introduction of new modern technology has significantly changed the landscape of plastic extrusion. It has actually resulted in the development of advanced extrusion equipment, which has boosted the effectiveness and top quality of the plastic extrusion procedure. Moreover, additional reading developments in the extrusion process have actually also been driven by technological developments, supplying enhanced capabilities and convenience.
Advanced Extrusion Machinery
Transforming the world of plastic extrusion, progressed equipment imbued with innovative innovation is ushering in a new era of efficiency and accuracy. These equipments, furnished with ingenious functions like self-regulating temperature level control systems, guarantee ideal conditions for plastic handling, consequently lessening waste and enhancing product high quality. While these developments are already impressive, the continual development of technology assures also better leaps forward in the area of plastic extrusion machinery.
Technologies in Extrusion Procedures
Harnessing the power of contemporary technology, plastic extrusion procedures are undertaking a transformative metamorphosis. With the introduction of 3D printing, the plastic extrusion landscape is likewise broadening right into brand-new worlds of opportunity. These technical breakthroughs are not only improving the top quality of extruded plastic products but also pushing the market in the direction of a much more sustainable, effective, and ingenious visit our website future.
Real-World Applications of Plastic Extrusion
Plastic extrusion, a functional and reliable procedure, discovers use in many real-world applications. It's mostly used in the production market, where it's used to create Read Full Article a myriad of products such as pipelines, tubes, home window frameworks, weather condition removing, and secure fencing. The auto sector likewise utilizes this technology to produce components like plastic and trim sheet. Additionally, the medical area depends on extrusion for the construction of catheters, IV tubes, and various other medical devices. Also in food manufacturing, extrusion plays a function in forming items like pasta or grain. The stamina and adaptability of plastic extrusion, paired with its cost-effectiveness, make it a vital process throughout different sectors, highlighting its widespread sensible applications.
The Future of Plastic Extrusion: Trends and predictions
As we look to the horizon, it becomes clear that plastic extrusion is positioned for substantial innovations and transformation. Eco-friendly choices to standard plastic, such as bioplastics, are likewise expected to obtain traction. These trends show a dynamic, developing future for plastic extrusion, driven by technical technology and a commitment to sustainability.

Verdict
In final thought, plastic extrusion is a complex process that utilizes innovative modern technology and varied materials to create varied items. As plastic manufacturing continues to evolve, it remains a vital part of numerous industries worldwide.
In significance, plastic extrusion is a high-volume production process in which raw plastic material is melted and created into a constant profile.While plastic extrusion is a commonly made use of method in production, the products used in this process greatly affect its final result. At its core, plastic extrusion includes transforming raw plastic product into a continuous profiled form. It has led to the growth of sophisticated extrusion equipment, which has enhanced the performance and high quality of the plastic extrusion procedure.In final thought, plastic extrusion is a complex procedure that makes use of sophisticated technology and differed materials to produce diverse products.
Comments on “Plastic extrusion for economical product fabrication”